Many friends of mine have asked me this question: why is silica sol casting so expensive? However, the only thing I can do is smile helplessly. It's a long story but a short story. Here I will explain the core value of silica sol casting.
First, as a buyer, you need to understand what casting is. Casting is all about smelting metal, manufacturing casting molds, and pouring molten metal into the casting molds. After solidification, there is a method for forming metal parts with a certain shape, size and performance. There are three types of casting method: sand mold casting method, metal mold casting method, and lost wax casting method.
Since our silica sol process is a kind of lost wax casting method, we will focus on the lost wax casting method.
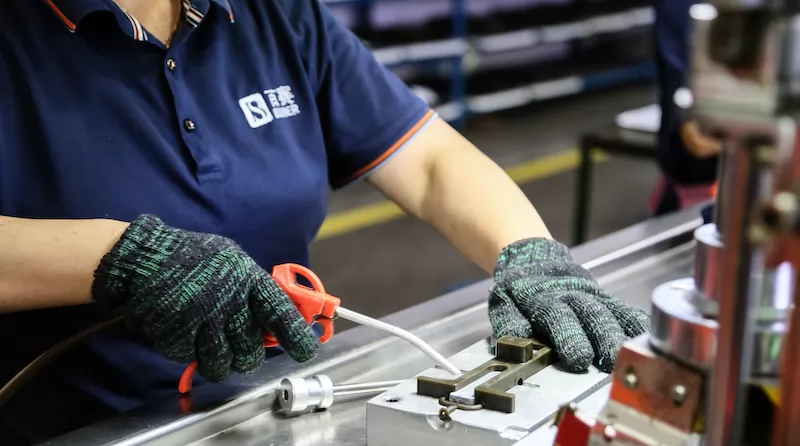
The lost wax casting method is simply to copy the object to be cast with wax, then immerse it in a pool containing sand/powder and let it dry, so that the wax replica is covered with a layer of sand film. The steps are repeated until the outside film is sufficient to support the casting process. Then the wax in the mold is melted and the mold is drawn away. After that, the mold needs to be heated many times to increase the hardness before it can be used for casting. This method has good accuracy, but because the price of sand/powder is quite high, and the production requires multiple heating and complicated, the cost is quite expensive.
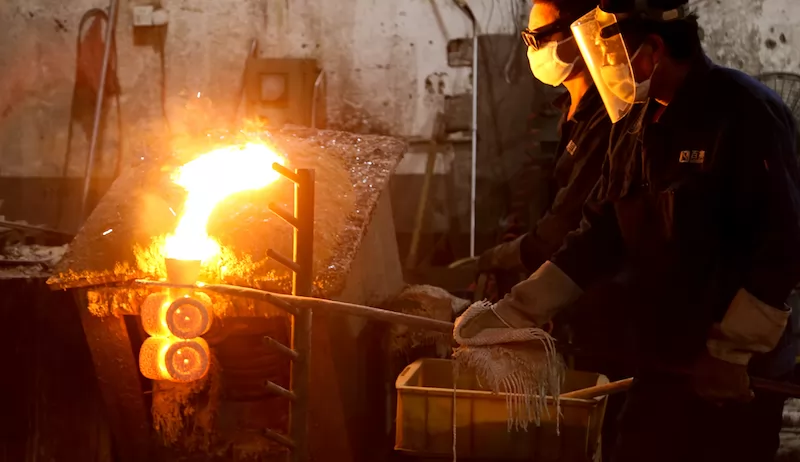
The surface roughness of the products cast by the silica sol process can reach Ra3.2-6.3. Because the casting blank is almost shaped, it achieves the purpose of avoiding mechanical processing or a small amount of processing, reducing the cost and reducing the production time to a certain extent.
There is also a more commonly used lost wax casting method that uses the water glass process, which has certain advantages in price compared to the casting water glass produced by the silica sol process, which means it is cheaper. Here is a brief analysis of the differences in the production process of the two processes.
Casting process: Water Glass Process
Surface roughness: Ra12.5-50
Wax injection equipment: uses domestic pneumatic equipment
Wax mold material: Water glass process uses domestic low-temperature wax, which is around 700 dollar per ton
Shell sand material: Water glass process uses domestic quartz sand and quartz powder
Dewaxing Equipment: Water glass process uses boiled water to dewax
Roaster: Water glass process generally uses a coal-fired roaster with a temperature of 900 degrees
Casting furnace: The water glass process generally uses a 400KG furnace
Casting process: Silica Sol Process
Surface roughness: Ra3.2-6.3
Wax injection equipment: Silica sol process uses imported hydraulic equipment
Wax mold material: Silica sol process uses imported medium-temperature wax, which is around 2900 dollar per ton
Shell sand material: Silica sol process uses imported zircon sand and zircon powder with higher mesh-
Dewaxing equipment: Silica sol process uses an electric dewaxing furnace to dewax
Roaster: Silica sol process uses an electric roaster whose temperature can reach 1100 degrees
Casting furnace: Silica sol is generally used in a small furnace of 150KG which has a fast casting speed and stable temperature
Above are products made through water glass process.
|
Above are products made through silica sol process.
|
The differences in the production process result in a big difference in the final product. The products produced by the silica sol process have higher dimensional accuracy and better surface roughness than the products produced by the water glass process. If you care about quality more, please respect its price; if you want a cheaper product, please accept its flaws! What you can get depends on how much you want to pay for it.
Finally, here is the summary of the core advantages of silica sol casting: good casting surface and high dimensional accuracy, which saves a lot of surface treatment time and size outsourcing processing. From the perspective of finished products, it actually reduces costs.
What kind of processes to choose depends on the specific needs of customers. One thing we want to let you know is that if you choose us Besser Casting, we will not let you down.
Core values of Besser Casting: treat people with sincerity, deal with things with perseverance, persist in innovation, keep learning, shoulder responsibility, and meet competition!
The goal of Besser Casting is to become an enterprise that truly continues to exist because of the value created, and is recognized and needed by the market and society!