BESSER offers high quantity lost wax investment casting solutions and services. Our in-house services include include ceramic mold making, advanced machining, heat treatment, and casting for multiple materials and project outcomes. We provide dimensional accuracy and precise components based on the specific needs of your project. Our large casting foundry, with unmatched industry experience, and access to advanced equipment give product innovators and project managers the ability to produce high quantity metal parts and components within the size and scope of budgets, timelines, and quality standards. I f machining is required, our one-stop shop can deliver surface finishing for complex geometry parts.
There are many benefits associated with lost wax investment casting. The enhanced flexibility of being able to utilize nearly any metal material makes this process suitable for a variety of industries and applications, including aerospace, energy, automotive and more. There’s also a great deal of room for flexibility, as investment casting can be executed using many different alloys, including tool steel, stainless steel, carbon steel. and low-alloy steel.
In addition to producing parts of intricate shapes and sizes, lost wax investment casting helps minimize material waste and conserve energy. It also provides manufacturers the ability to cast complex parts with superb surface finishes, greater dimensional accuracy, and no flash or parting lines.
Investment Casting Manufacturer
Looking for an innovative Investment Casting partner? One that provides outstanding service, exceptional quality, and low costs - all within short lead times? Look no further than Besser Casting, Inc. for your casting needs.
Investment Casting Products We Have Done for Customers
Besser handles each job with an optimal process to achieve the lowest cost, best quality, and highest efficiency.
Investment Casting Foundry
Besser Casting, Inc. is China's leading precision investment casting foundry, which began manufacturing investment castings in 2001. Throughout our history, we have been proud to partner with our customers to solve their casting problems in innovative, cost-effective ways. .
Whether you require complex cast components weighing just a few grams or large components of up to 50 pounds, or your needs include high volume, rapid prototype, or short-run projects, you can count on the experience, innovation, and dedication of Besser Casting to work for you.
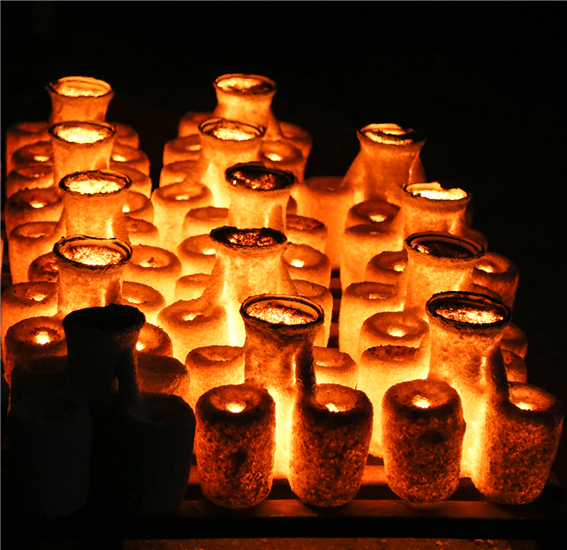
Full-Service Casting Capabilities
I have a full-service foundry in China that can meet your custom needs. By partnering with us on your investment casting project, you'll benefit from the experience and capabilities of an industry leader.
Besser Casting, Inc. offers a variety of services to ensure the quality and longevity of all of our investment cast products. Our heat treatment solutions include machinability annealing, material stress relief normalizing, and durability and wear hardening. To ensure quality, we perform non-destructive testing such as X-ray, Class A X-ray, HIPing (or Hot Isostatic Pressing), Magnetic Particle Inspection and Fluorescent Penetrant Inspection.
As for the custom finishing touches, Besser Precision Casting, Inc. handles all plating and finishing. This includes phosphate coating, polishing, hand polishing, passivation, pickling and electropolishing.
Provide Our Customers with the Best Molding Solutions
We are Committed to Delivering the Highest Quality Investment Castings.
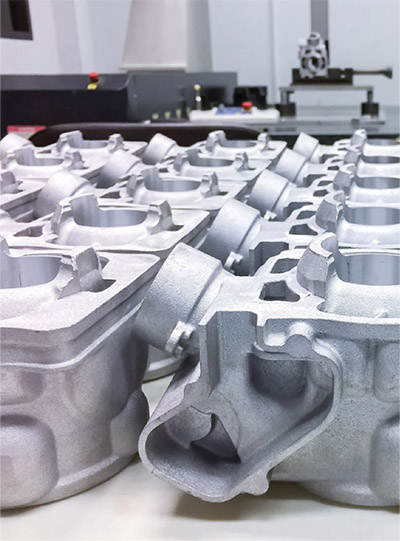
Castings for the Automotive Sector
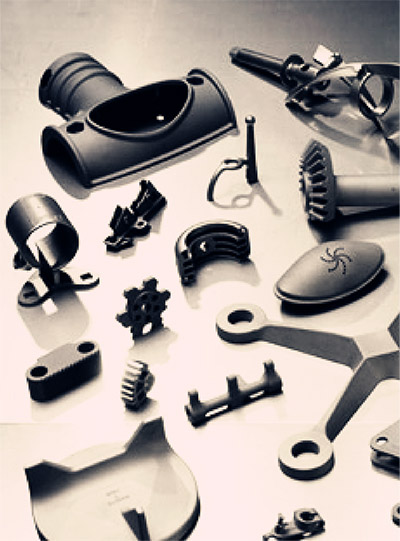
Construction Hardware Casting
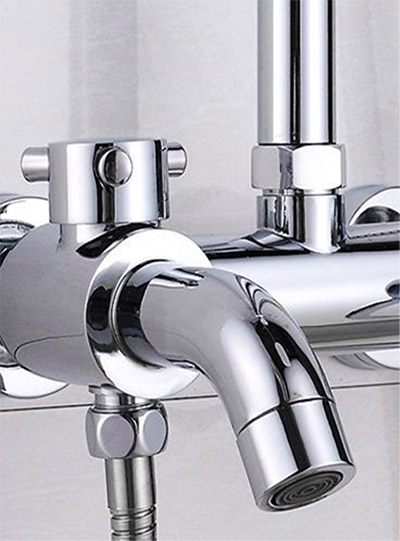
Bathroom Hardware Casting
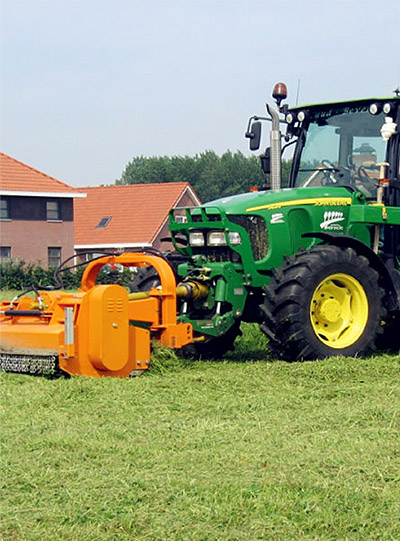
Agricultural Equipment Casting
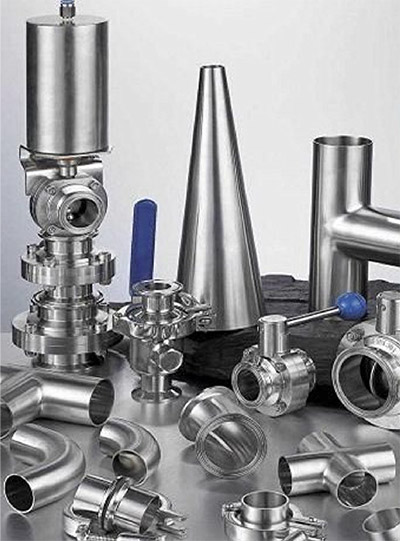
Hydraulic Equipment Casting
Fortune 500 Companies Choose to Cooperate with Us
Custom Investment Casting Frequently Asked Questions
Q1: What is an investment casting process?
A1: Investment casting is a manufacturing process in which a liquid material is poured into a ceramic mold, which contains a hollow cavity of the desired shape, and then allowed to solidify. The solidified part is the casting, which is broken away from the ceramic mold to complete the process.
Q2: How accurate is investment casting?
A2: Quite Expensive: Investment casting is quite costly compared to other processes. This is especially true when dealing with a low volume of production. Labor Intensive: As the process is complex and involves a lot of steps, it is quite labor-intensive. So, the labor cost is high for precision casting.
Q3: Is investment casting expensive?
A3: Investment casting is preferred for its ability to produce complex and intricate parts with high precision. It offers excellent surface finishes and allows for the casting of thin-walled sections, reducing the need for secondary machining.
Q4: Why is investment casting costly?
A4: Investment casting, also known as lost-wax casting, allows for the creation of intricate and detailed metal parts. Factors that affect investment casting costs are hard tooling, casting size, casting shape, alloy material, quality requirements, dimensional requirements, and quantity.
Q5: What is the size limit for investment casting?
A5: Investment casting is used with almost any castable metal. However, aluminium alloys, copper alloys, and steel are the most common. In industrial use, the size limits are 3 g (0.1 oz) to several hundred kilograms. The cross-sectional limits are 0.6 mm (0.024 in) to 75 mm (3.0 in).
Q6: What kind of wax is used in investment casting?
A6: Paraffin wax is used to affect the rheological properties, the injection temperature and fluidity of the investment casting wax material. Microcrystalline wax is also a hydrocarbon based petrochemical produced as a by-product of the distillation of crude oil.
Q7: What products are made by investment casting?
A7: The applications of investment castings are limitless. However, the aerospace, power generation, firearm, automotive, military, commercial, food service, gas and oil, and energy industries use these metal components the most.
Q8: Why do people use investment casting?
A8: Investment casting is generally used for making complex-shaped components that require tighter tolerances, thinner walls and better surface finish than can be obtained with sand casting. The distinguishing feature of investment casting is the way the mould is made.
Q9: What is the difference between casting and investment casting?
A9: Investment casting accommodates both ferrous and non-ferrous metals, while die casting is only suitable for non-ferrous casting metals. Investment casting is ideal for low and medium-volume production runs, while die casting is more appropriate for high-volume production runs.
We are a non-standard custom factory and do not have our own molds. The existing more than 3,000 pairs of molds are owned by customers. We only store them on behalf of customers, so we cannot use customers' molds. If you need to develop products, you can only develop new molds.